Before deciding to use these PTFE coating, you should know what they are, their properties, safety level, unique types, how the process of coating is applied, applications, etc.
So, if you want to learn all these read this guide.
What are PTFE Coatings?
These are special types of coating known for their unique non-stick properties. The coating consist of mainly fluorine-carbon bonds.
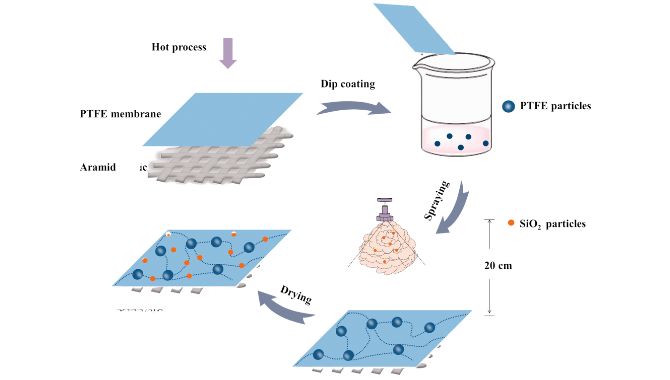
Why are Benefits of PTFE Coated Products?
The benefits of PTFE coated products abound. However, these benefits makes this coating process unique. These benefits include:
Resists Friction and has Low Abrasion
Teflon coating surfaces come with low coefficients of friction, ranging between 0.04 and 0.15. It works perfectly for stud bolts, nuts, bearing surfaces, shafts, moving mechanisms, and fasteners. This is because it persists where grease or oil disappears at very high temperatures.
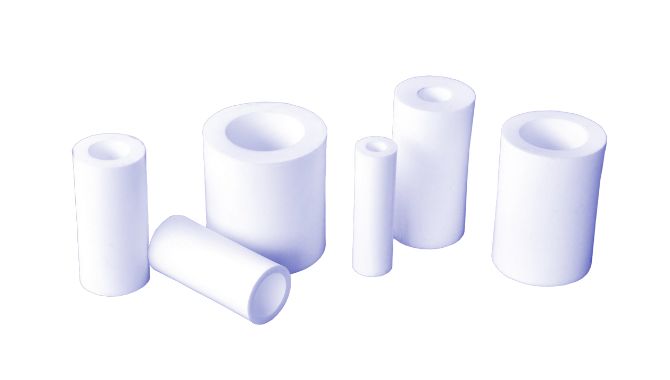
Non-stick
Components with PTFE coating have great non-sticking properties. Due to that, they are easy to clean. These coatings are used more in bakeries, the cookware manufacturing industry, food processing sectors, etc. No matter the type of food, they cannot stick in the pans or cookware equipment.
Anti-galling
Galling is prevented when xylan coatings are applied to surfaces. This is where mating surfaces as well as spinning components gain too.
Resists Temperature
Extreme temperature application conditions are no match for Teflon coatings. PTFE coatings are able to stay steady even at higher temperatures of +260°C and +290°C for brief periods.
Non-wetting
PTFE coatings makes surfaces they are applied on oleophobic resistant. Due to this, they are beneficial to the semiconductor sector. They have hydrophobic wettability resistant features too.
Good Electrical Insulation Properties
You will find Teflon coating used to insulate different wires and electrical parts. This is because they have high dielectric strengths, low dissipation features, etc. These coatings are ideal for light fixtures, cable guides, connectors, including handheld electrical devices.
PTFE Coating Properties
Thermal Properties
- Max temp use continuously 500°F
- Max temp use intermittent 550°F
- Thermal Conductivity 1.7
Electrical Properties
- Dielectric Strength of 16 volts/micron
- Volume resistivity of 1.0E+18 ohm/c
- Surface Resistivity of 1.0E+18 ohm/Sq.
Physical Properties
- Specific Gravity 2.2
- Water Absorption of <0.01
Chemical Properties
Is PTFE Coating Safe?
When it comes to evaluating the safety of Teflon coating, it is important to note the following:
- Chemically inert. Due to its chemically inert nature, it won’t interact with any other chemicals in or on your body.
- Its low coefficient of friction feature also makes it food safe.
- PTFE coatings are harmless and won’t hurt you if you eat it. There are no health dangers associated with eating food that contains flaking or chipped pan pieces as they move through your digestive system.
- PTFE is FDA approved and food grade safe.
You can learn more about: PTFE safety.
Types of Teflon Coating
The formulations of PTFE coating on specific applications and uses.
Some common options include:

PTFE Powder Coating.
Mostly in the form of powder, they are ideal for different uses like breathable hydrophobic membranes, high performance cables and wires, and aerospace / automotive hoses. They are perfect for medical applications too.
PTFE Spray Coating
This is a solvent-based type of Teflon coating ideal for various industrial applications. It is easily able to withstand abrasions and is highly durable.
Colored PTFE Coating
Naturally, PTFE coatings come in colors grey or black. When different fillers are added to Teflon, it can end up in different colors. Mostly, you will find Teflon PTFE coating in the following colors such as black PTFE coating, grey PTFE coating or blue PTFE coating, just to mention a few.
How PTFE Coating Applied?
Below is a step by step method on how PTFE coating process is done:
Step 2: Prepare Surface for PTFE Coating Process
Here, you will need to ensure the surface or the component to be coated has a smooth and even surface. This helps to simplify and make the coating process very fruitful in the long run.
Step 3: Heat Cleaning Process
Next, heat cleaning the product to be coated is important. Heat cleaning should be done at +400°C. This needs to be done to get rid of all grease or oil present that can hinder the smooth coating process.
Step 4: Grit Blasting
After heat cleaning is done, the product surface is grit blasted. This is done to get rid of old coating or even ensure the needed profile is obtained for a brand new PTFE coating to be done.
Step 5: Coating Parts with PTFE
Use the ideal coating on the product (spraying or dipping) to the specific thickness. There are times when you will need to have multiple applications. The coating types can be in dry powder or wet spraying form.
Step 6: Curing Process
Finally, the product that has been coated needs to be cured. Curing needs to be done for a specific time from 150 and 420°C based on the specific coating.
Applications of PTFE Coating
Today, we use PTFE coated product in many applications. Let’s look at some common uses:

PTFE Coated Fiberglass Fabrics
PTFE coated fiberglass fabrics are used more in making belts used for the movement or transporting of food items in the food processing industry.
PTFE Coated Bolts and Nuts
These components are used in bolting industries, outdoor equipment manufacturing industries, food processing plants, medical device production, etc. They are generally known fasteners.
PTFE Coated Nozzle
These types of nozzles are used in different industries like chemicals, food, and pharmaceuticals.
PTFE Coated Glass
If you want to improve performance of glass, you can apply Teflon coating.
PTFE Coated Cookware
They are ideal for heat-resisting and PTFE non-stick coatings on pans, pots, and some other cooking appliances such as coffee makers, waffle makers, etc. They are used a lot in the food and beverage industry.
PTFE Coated O-rings
PTFE coated O-rings are used a lot in the electrical or electronic, automotive, mechanical, medical and marine industries.
PTFE Coated Screws
These are also categorized as fasteners. They are used more in the electrical industries for semiconducting and also in pharmaceutical manufacturing as well as hardware industries, etc.
PTFE Coated magnets
Teflon coated magnets are a valuable part in industrial production equipment like liquid pipeline separators, electromagnetic filters, as well as metal detectors.
PTFE guide wire
Teflon guide wires are insulated wires used in the industrial, military, electronics aerospace, and other commercial industries.
PTFE Coated Pipe
PTFE insulated pipe systems are used in nearly all petroleum, chemical, food, pharmaceutical, and other sectors that handle extremely toxic and dangerous acids and solvents for processing needs.
PTFE Coating for Cars
There are many car parts and component are highly corrosion resistant. They can withstand heat and resist high temperature.
Conclusion
Teflon’s non-stick feature makes it famous. They are used in various industries to achieve the highest level of product protection needs. That is why knowing more about these coatings helps you decide on how they can be used for your good.